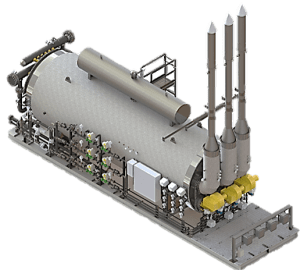
ABOUT EQUIPMENT
INDIRECT-FORCED FRAUGHT WATER BATH HEATER
PEPCO A process bath heater is a simple and safe systems for indirectly heating various process mediums. A bath solution is heated by a firetube style burner submerged at the bottom of the heater vessel. The bath solution then heats a submerged process coil, in which the flowing process medium is heated.
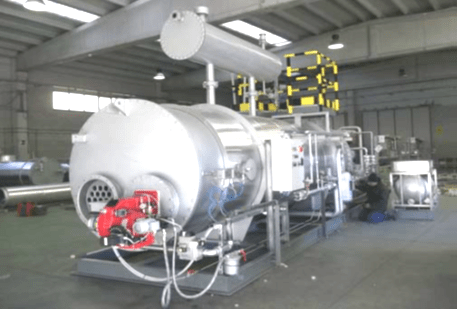
INTRODUCTION
PEPCO divisions specialize in the design and supply of oil & gas equipment and transmission systems with powerful traceable documents. Complete systems are generally supplied as fully assembled, painted and tested according to latest edition of standards. Quality is controlled by the advanced methods of Non-destructive tests, Inspection is carried out with calibrated instrument and computerized calculations.
PEPCO has a wealth of experience in supplying equipment. Equipment’s are designed and engineered in-house by engineer teams using advanced software.
PEPCO is fully committed to quality and all in-house procedures are in full accordance with ISO. An individual inspection control plan is produced for each critical component is monitored by inspectors with ASNT, ASME, AWS, AISC certificates.
INDIRECT WATER BATH HEATER OPERATION
The process coils and the fire tubes are immersed in a water or liquid bath. As the unit is fired, heat is transferred from the fire tube to the liquid bath and then to the process fluid. The use of a bath promotes uniform heating and reduces the chance of hotspots. Due to the indirect nature of bath heaters the safety risks are much lower (combustible streams isolated) compared to direct fire-tube heaters, they can therefore be used in hazardous areas where safety is a concern.
Water Bath Heaters are indirect fired type heaters specifically designed to meet the precise requirements of any process application and customer or regulatory specifications such as API 12K and/or other international codes. These devices are traditionally used to heat natural gas and oil. They were horizontally mounted.
These heaters have a wide variety of successful applications such as:
- Gas dew Point Heating: high-pressure natural gas heating upstream pressure regulation stations preventing condensation phenomena.
- Heating of high-pressure natural gas upstream pressure regulation in order to prevent external icing formation.
- Fuel Gas super-heating upstream gas turbines (Performance Heaters).
- Gas Heating downstream low temperature storages.
- Hydrate prevention.
- Viscosity reduction: Crude Oil Heating upstream treatments to facilitate degassing and dewatering.
- Vaporizing and superheating LPG & LNG
- Heat sensitive gas and fluids
GENERAL INFORMATION
For gas well heads and pipelines, a large reduction in pressure will cause a substantial temperature drop in the gas. This phenomenon is known as the Joule-Thompson effect, therefore with a loss of temperature of approximately 5°C for each 1000kPa reduction in pressure.
Usually the bath fluid is water but depending on the climate and heating requirements. it can also be oil (capable of heating process fluids to higher temperatures) or a mixture of water and glycol (used in colder climates to lower the freezing point).
The natural gas must be heated so after any pressure reduction the temperature must be above freezing and hydrate point. Subzero temperatures can result in embrittlement of piping and fittings, formation of ice and the formation of hydrates within the pipe with a potential for blockage of filters and regulator valve seats and others. Therefore, heating with a Water Bath Heater (WBH) is commonly applied before pressure reduction of natural gas.
delivery program includes Indirect Water Bath Heaters for different applications and duties using Water and Water-Glycol as heat transfer media. PEPCO Bath Heaters are specifically designed to meet the precise requirements of any process application and customer or regulatory specifications such as API 12K and/or other national/international codes.
PRINCIPLES OF COMPONENT
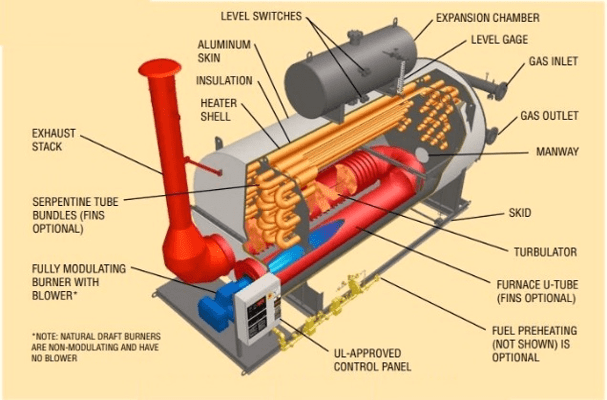
Water bath heaters are composed of the following main components:
- Body or Shell
- Coil or U tube bundle
- Water expansion tank
- Fuel feed line
- Burner
- The fire-tube
- Stack
- Skid frame & platform
- Burner management system panel (BMS)
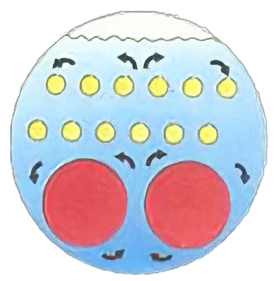
Shell is an atmospheric vessel designed in accordance with API-12K requirements containing the process coil, fire tubes and heat media. The heater shell contains the fire-tube that allows rapid heat transfer (both radiant and convective) from the flame to the hot medium.
The heat is transferred from the bath to the coils/tube bundle and then safety to the gas or the oil. In order to completely use the water bath free convection, the firebox and the flue gases tube bundle are positioned beneath the high-pressure coil.
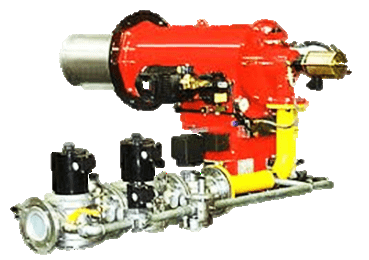
Based on working conditions and power availability on the operating site the burner is categorized to forced or natural draught. Forced draught burner are ideal whenever there is a low emission requirement, utilizing small bore fire tube reduce the “dead gas film” region along the tube walls.
This results in a reduced tube area compared to their large bore counterparts, therefore, more compact heater available and also making fine-tuning the air/fuel ratio possible to achieve more efficient combustion. It is ideal for applications that require lower flux rates to prevent fluid damage or coking.
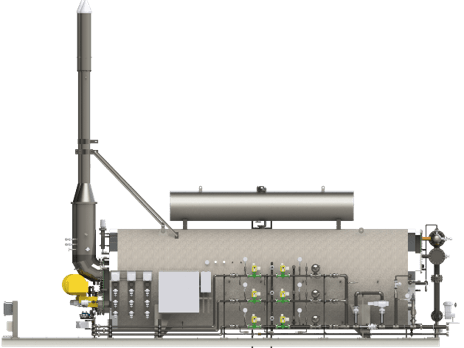
The expansion Tank allow the hot medium to be contained for the thermal expansion due to the temperature increase level gauges and transmitters advise when additional or hot medium is required and give alarm in case of overfilling. Reduces corrosion in the heater shell by keeping it liquid-packed and moving the wet-dry interface of the expanding bath media into the expansion tank.
Petroleum-based fuel is a widely used source of energy around the world also the use of gas-fired plant in industry is now increasing rapidly and it is necessary to ensure that all this plant will operate with a high standard of safety. The most important requirement for ensuring safety when using any fuel is that of the prevention of explosions and fires.
Appropriate control systems and good burner designs normally preclude the accumulation of sufficient fuel in a plant to cause a hazardous pressure rise in the event of ignition. Whilst every effort is made to make such systems “fail safe”, in the event of a multiple fault situation, involving perhaps mal-operation of the plant, an explosion hazard could arise.
Sample NUMBER
Indirect Forced Draught Water Bath Heater
Burner constitutes of auto ignition-fuel control-flame sensing systems. It comprises of a burner, combustion blower, gas train and an electrical control panel. These burners are suitable for Natural gas, LPG, Biogas and allied gaseous fuels.
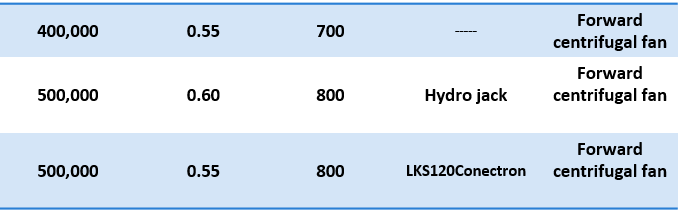
TYPE DESIGNATION
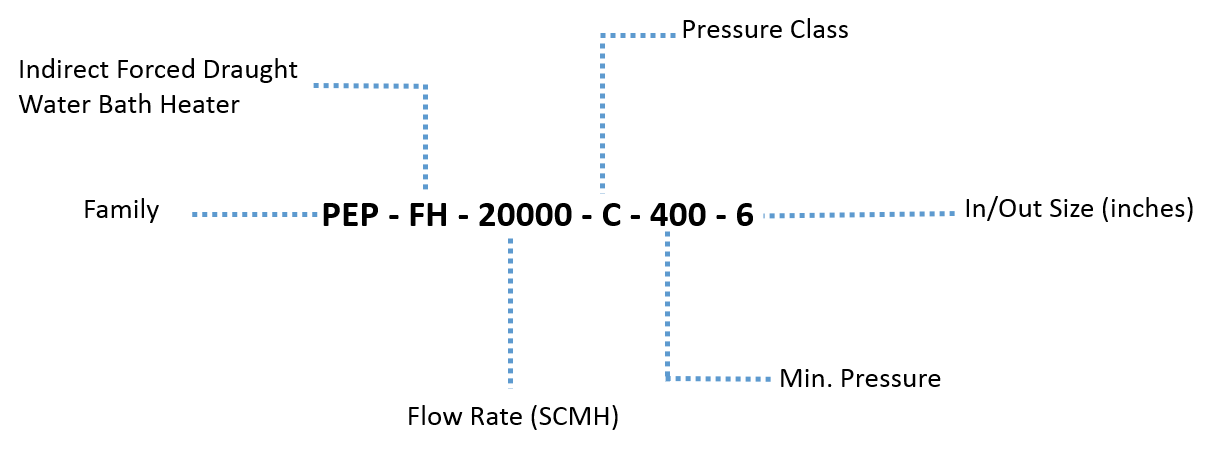
FEATURES
Indirect Forced Draught Water Bath Heater
- Standard Features
- Standard Features
- Body or Shell
- Removable fire tube
- Standard or engineered burner configurations
- Forced draught burner
- Thermostat
- High efficiency burner system
- Flame arrestors
- Safety shut down
- Complete control systems
- Fuel shut down valve
- Insulation
- Primer (1 Coat) + Enamel Paint (2 Coats)
- Removable flow coil
- Fuel gas preheat coil
- Fuel gas system c/w piping, filter, valves & Instruments
- Fire tube stack
- Optional Features
- Standard Features
- Body or Shell
- Spark arrestors
- Skid mounting
- Alarm systems
- Dual temperature control
- Full process automation / BMS
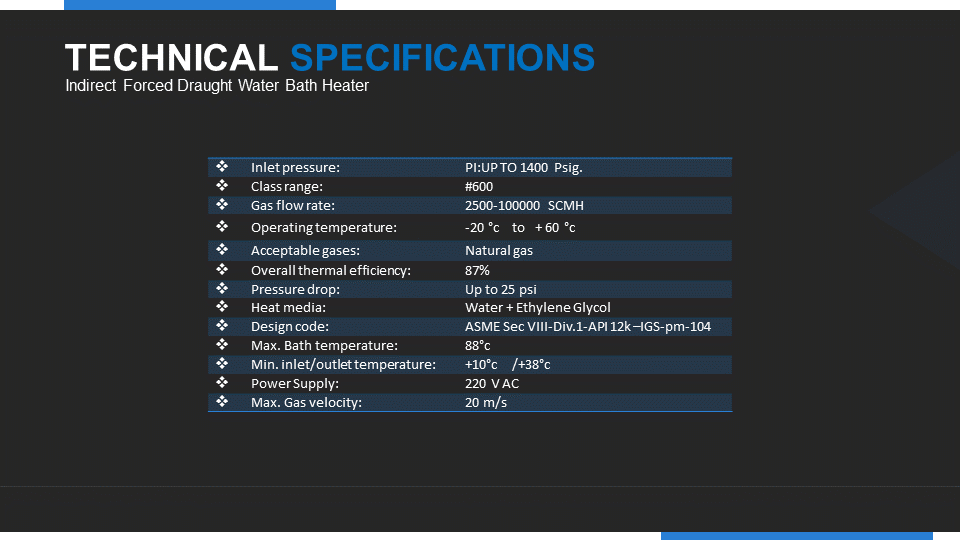
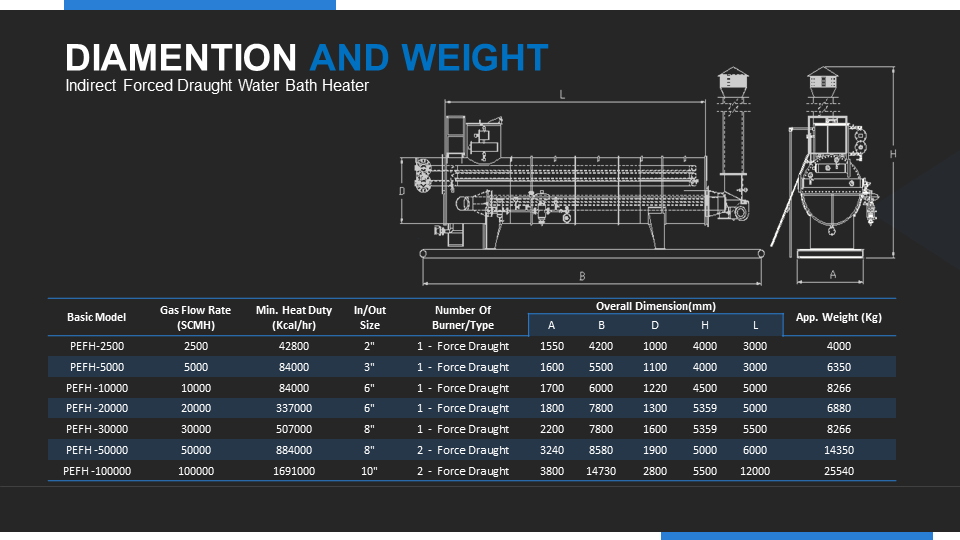

