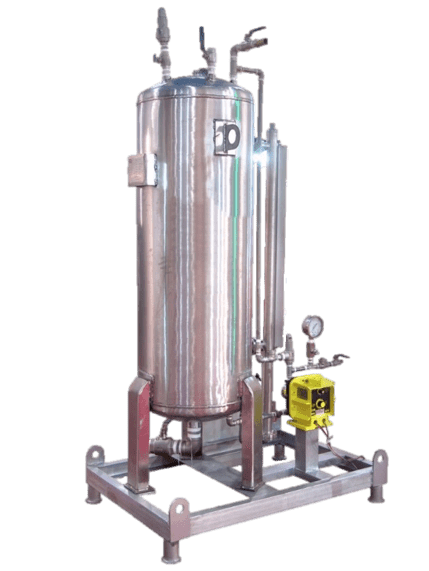
ABOUT EQUIPMENT
INJECTION ODORIZER
PEPCO Injection Odorizer are pneumatically powered, solenoid driven or positive displacement specifically designed for gas transmission industry to inject smell of a skunk into the gas without getting any odor on yourself or stinking up the area.
ABOUT EQUIPMENT
PEPCO Injection Odorizer are pneumatically powered, solenoid driven or positive displacement specifically designed for gas transmission industry to inject smell of a skunk into the gas without getting any odor on yourself or stinking up the area.
PRINCIPLESOF OPERATION
The flow diagram below showing the principle of operation .the measuring element (Gas Meter) used to determine the flow of gas in the main pipeline. As the control box of odorizer, accumulate all signals from gas meteres, it will send a signal to the pump (adjustable) for odorant discharge. .
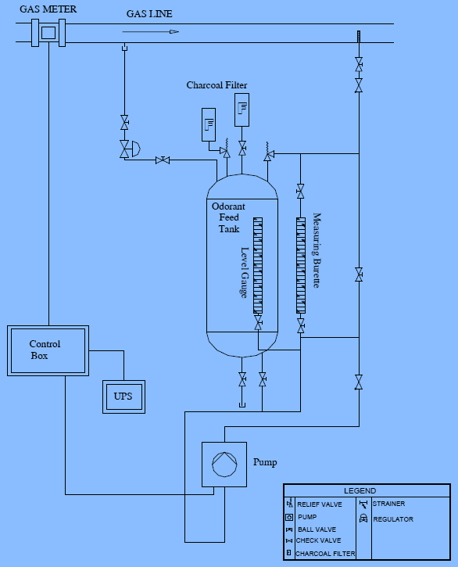
QUICK OPENING CLOSURE
almost any range of gas flow and can be specially designed for pressure as high as 1200 to 1500 PSIG without any difficulty. .
TYPE DESIGNATION
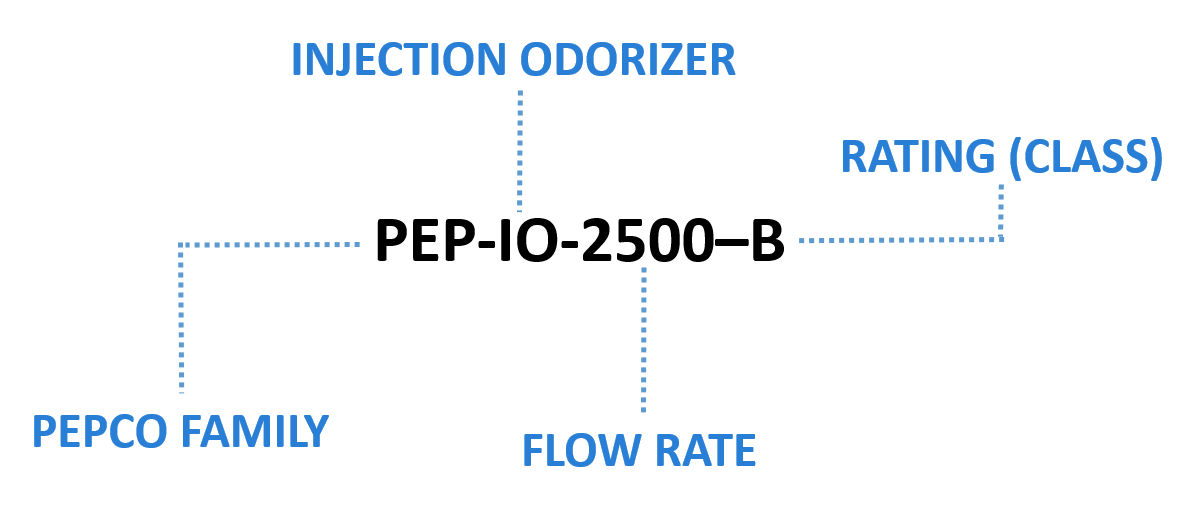
Injection Odorizer Troubleshooting
Low pump out put
Low pump output can be caused by many things. The some of the more common ones are:
-
- Very low stroke setting
Check position of stroke length knob by rotating until diaphragm stopes moving with the pump operating. the diaphragm should not stop reciprocating until the knob points to zero, reset knob by grasping the knob and pulling it towards you. pry the yellow cap off of the knob. place the knob on a flat surface. using needle nose pliers, squeeze the inner section together while lifting outer section up.
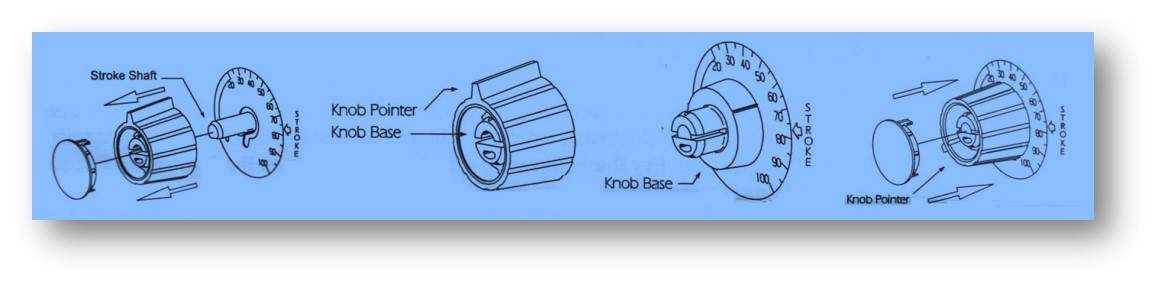
Push the inner section back onto the “d” shaped stroke shaft with the pump running , zero the pump by turning the inner section of the knob counter clockwise. position the outer section of the knob so that the pointer aligns with zero on the Name Plate. push down on the outer section of the knob .replace the yellow cap over the outer section of the knob, aligning the tabs on the cap with the slots on the knob.
-
- Trapped air in pump head
may be caused by leaks in the suction line, where the suction line joins the suction fitting, or at the seal ring between suction fitting and pump head. it may also be caused by air or gases coming out of solution. trapped air or bubbles in the discharge line have no effect on the pump`s operation. they may be ignored. To remove trapped air from the pump head , operate the pump with stroke frequency knob and stroke length knob set at 100.
-
- Air leak through valve seal rings
usually cause by worn or damaged seal rings or loose fittings. tighten fittings by hand until they are very snug. if there is no improvement, replace both seal rings in pump head.
-
- Ruptured pumping diaphragm.
if rupture is severe and pump is injecting into pressure, solution leak will be obvious through the diameter hole at the bottom of the spacer directly behind the pump head.
-
- Clogged liquid end, or injection point connection
will cause low pump output. purge liquid end, disassemble liquid end, clean individual parts with water and detergent.
Excessive pump out put
Syphoning
If your pump has a liquid end other than a high viscosity le, its injection check valve assembly has a chemically resistance antisyphone spring . disassemble the injection check valve and check to be sure this spring is in place and undamaged. replace if necessary.
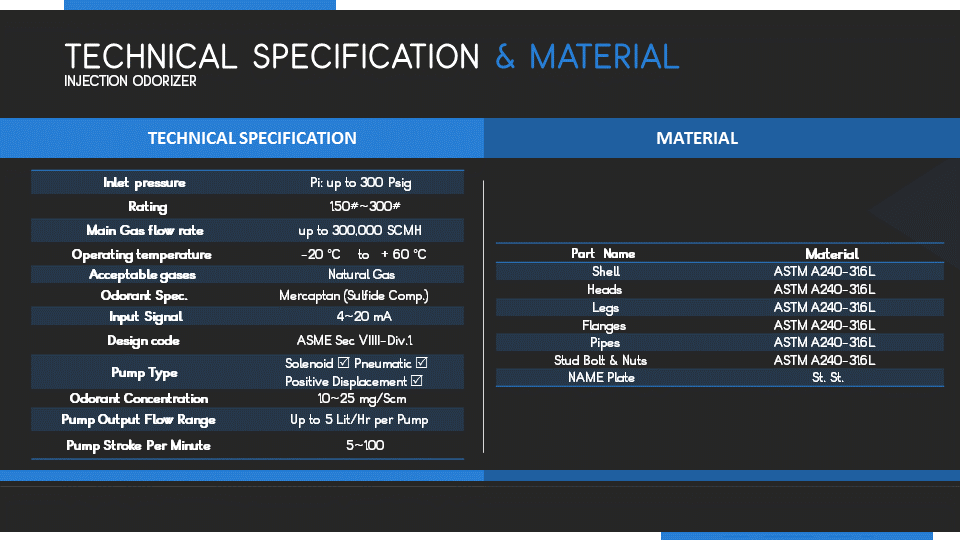
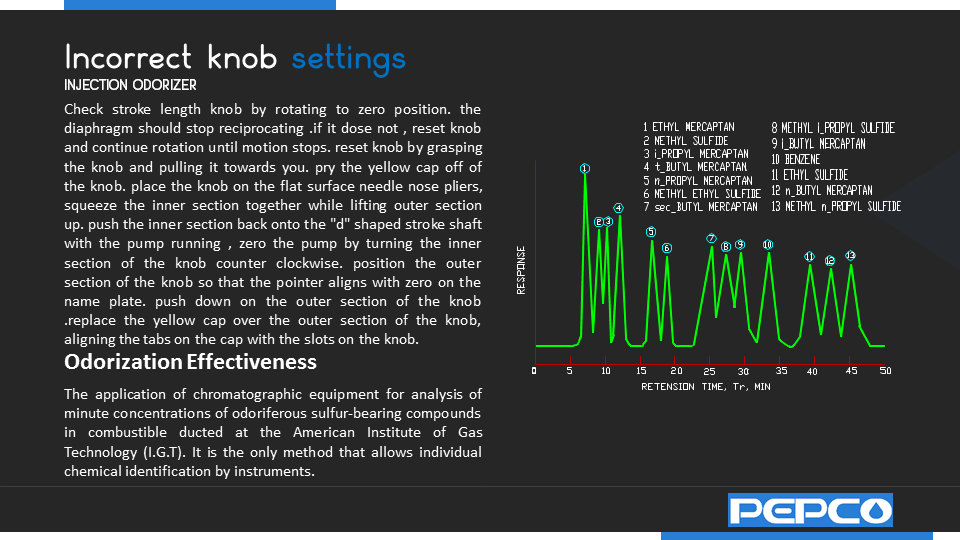