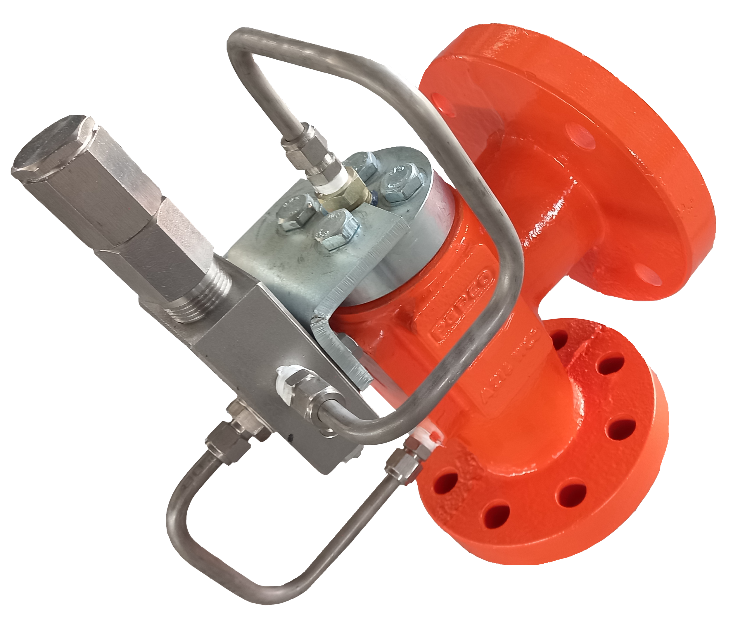
ABOUT EQUIPMENT
SAFETY RELIEF VALVE (Pilot Operated Type)
EQUIPMENT
PEPCO features a non-flowing modulating pilot design. Capacities are certified by the National Board of Boiler and Pressure Vessel Inspectors for air, gas and liquid services.
All modulating pilot is of all stainless steelstandard construction and mounts on top of the same main valve. This pilot is available for pressure ranges from ANSI Class 150 to 600. Above 500 psig set pressure, the pilot sensing diaphragm is replaced with a piston seal. All other parts, with the exception of the range spring, remain the same.
The Style pilot operated pressure relief valve opens in proportion to the amount by which the system pressure exceeds the set pressure. This pressure difference is termed “overpressure”.
As overpressure increases, the opening of the main valve also increases until it is fully open. This occurs when theoverpressure is approximately 5 percent of set pressure. When the overpressure drops, the process reverses and the main valve gradually closes until fully closed at slightly below set pressure.
Operation
The system pressure communicates from Chamber A to Chamber C (the sense chamber) through the sense line. This pressure in Chamber C acts on the diaphragm to create an upward force, opposing that of the range spring. Until the set pressure is reached, this upward force is insufficient to overcome the spring force and the diaphragm assembly and attached parts remain in the extreme downward position. Under these conditions, the fluid pressure from Chamber C is transmitted down through Chamber D, past the inlet valve, and through Passage E into the main valve dome, Chamber B. This pressure acting, down on the upper area of the main valve disc generates a force greater than that of the system pressure in Chamber A acting upward on the smaller underside area of the disc. The net unbalanced force is downward, holding the main valve disc closed.
Standard Following
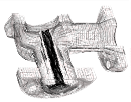
- Sizing: API 520
- Design & Mfg.: API 526
- Testing: API 527
- Code: Asme Section VIII Div.1
- ASME B16.5
- ASME B16.34
- Nace MR 0175
Applications
- Precession Pressure Control in Oil & Gas Industries
- Chemical Plant / Cryogenic Service
- Air, Gas, Vapor, Stem & Liquid Service
- Used in the system when Back Pressure is very high [ More Than 50% ]
- Used when Working Pressure & Set Pressure tolerance is very close
Benefits of POSRVs
- They compensate for variable backpressure up to 90% to 100% without the use of vulnerable bellows, which means they open and close at the exact set pressure regardless of the backpressure.
- Achieve their rated capacity at set pressure, not requiring any overpressure, which means they minimize product and energy loss and reduce environmental impact.
- Have independent opening and blowdown adjustments, which means they can be fine-tuned to match the specific conditions of the application.
- They have a large range of blowdown adjustment to overcome inlet piping losses, which means they can be installed further away from the process without compromising their accuracy.
- They are less prone to spring fatigue, corrosion, and fouling, which means they have longer service life and lower maintenance costs.
- Allow for in-line functionality testing possibilities, which means they can be verified without removing them from the system.